Compliance with safety regulations is a crucial aspect of running a business that involves lifting operations and lifting equipment. The Lifting Operations and Lifting Equipment Regulations (LOLER) are a set of regulations designed to ensure that all lifting operations are properly planned, supervised, and carried out in a safe manner.
If you are in an industry that involves any form of lifting, understanding and complying with LOLER is not just a legal requirement but also a fundamental component of maintaining workplace safety. For those looking to ensure they meet these requirements, a LOLER testing company can provide thorough examinations and certifications to help you stay compliant.
What is LOLER?
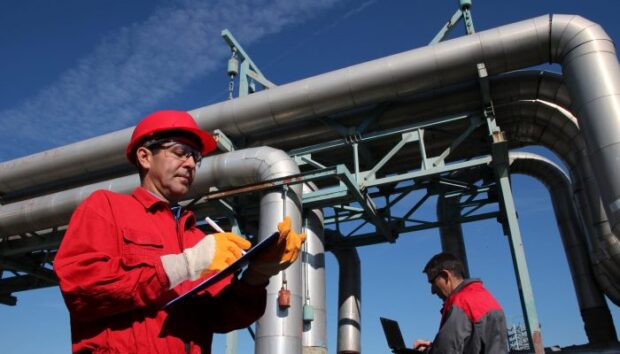
LOLER, or the Lifting Operations and Lifting Equipment Regulations 1998, is legislation in the United Kingdom aimed at minimizing risks associated with the use of lifting equipment in workplaces. These regulations require that all lifting operations involving lifting equipment are properly planned by a competent person, appropriately supervised, and carried out in a safe manner. LOLER applies to a wide range of industries and equipment, including cranes, lifts, hoists, forklifts, and even patient lifts in healthcare settings.
Key Requirements of LOLER
Understanding the key requirements of LOLER is essential for ensuring compliance. One of the main aspects is the requirement for thorough examinations of lifting equipment. These examinations must be carried out by a competent person at regular intervals, typically at least once a year, although the frequency can vary depending on the type and usage of the equipment.
The examination process involves a detailed inspection to ensure the equipment is in good working condition and safe to use. Any defects or issues identified during the examination must be addressed promptly to prevent accidents or equipment failure. In addition to regular examinations, LOLER also requires that lifting equipment be marked with its Safe Working Load (SWL) and that all lifting operations are properly planned and risk-assessed.
Competent Persons and Their Role
One of the critical components of LOLER compliance is the role of the “competent person.” A competent person is someone who has the necessary skills, knowledge, and experience to carry out thorough examinations and inspections of lifting equipment. This person must be able to identify potential hazards and assess whether the equipment is safe to use.
Planning and Supervising Lifting Operations
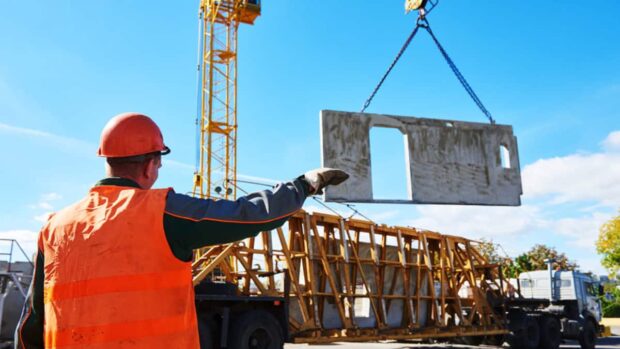
LOLER places a strong emphasis on the planning and supervision of lifting operations. Proper planning involves conducting a thorough risk assessment to identify potential hazards and determine the safest way to carry out the lifting operation. This includes selecting the appropriate lifting equipment, ensuring it is in good condition, and verifying that it is suitable for the task.
Supervision is equally important to ensure that the lifting operation is carried out safely. A competent supervisor should oversee the operation, ensuring that all safety protocols are followed and that any issues or concerns are addressed promptly. This includes monitoring the operation to ensure that the lifting equipment is used correctly and that the load is secure.
Ensuring Operator Competence
Operator competence is another critical aspect of LOLER compliance. Operators must be adequately trained and competent to use lifting equipment safely. This involves providing appropriate training and ensuring that operators have the necessary skills and knowledge to carry out lifting operations safely.
Training should cover various aspects, including the safe use of lifting equipment, understanding the equipment’s limitations, and recognizing potential hazards. Regular refresher training is also important to ensure that operators stay up-to-date with the latest safety practices and regulations.
Record Keeping and Documentation
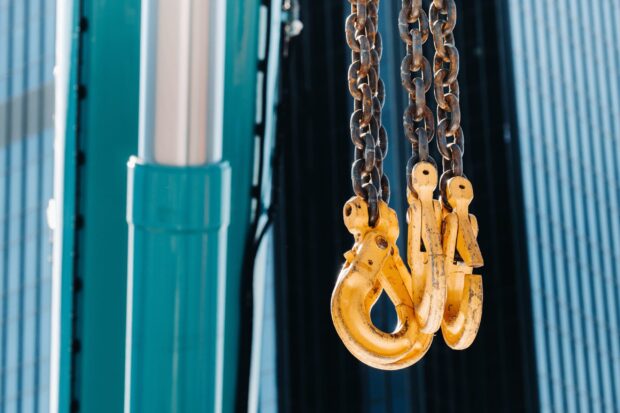
Maintaining accurate records and documentation is a key requirement of LOLER. This includes keeping records of all thorough examinations, inspections, and maintenance activities. These records should be readily available for review and should provide a detailed history of the equipment’s condition and any issues that have been identified and addressed.
Proper documentation helps demonstrate compliance with LOLER and provides a valuable resource for identifying trends and potential areas for improvement. It also ensures that any issues are tracked and resolved promptly, reducing the risk of accidents and equipment failure.
Addressing Common Challenges
Complying with LOLER can present several challenges, particularly for businesses with a large number of lifting operations and equipment. One common challenge is ensuring that all equipment is regularly inspected and maintained. This can be addressed by implementing a robust maintenance schedule and ensuring that inspections are carried out by competent persons.
Another challenge is ensuring that all operators are adequately trained and competent. This can be addressed by providing comprehensive training programs and regular refresher courses. Additionally, maintaining accurate records and documentation can be time-consuming, but it is essential for demonstrating compliance and identifying areas for improvement.
The Benefits of LOLER Compliance
While complying with LOLER can require a significant investment of time and resources, the benefits far outweigh the costs. By ensuring that all lifting operations are carried out safely and that lifting equipment is in good working condition, businesses can reduce the risk of accidents and injuries. This not only helps protect employees but also reduces the risk of costly downtime and repairs.
How to Get Started
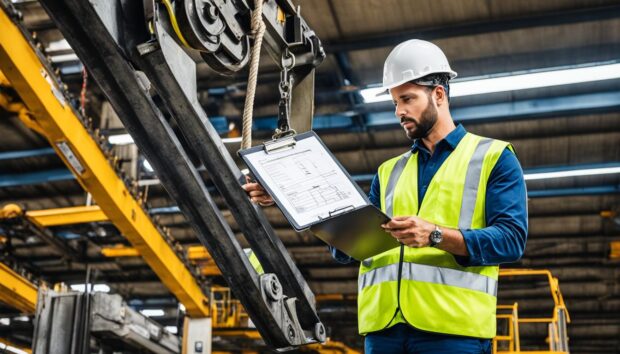
If you are new to LOLER or looking to improve your compliance, the first step is to familiarize yourself with the regulations and understand your responsibilities. This involves reviewing the key requirements of LOLER and assessing your current practices and procedures.
Next, identify any gaps or areas for improvement. This might involve conducting a thorough audit of your lifting operations and equipment, reviewing your training programs, and ensuring that you have competent persons in place to carry out inspections and examinations.
Staying Up-to-Date
LOLER is just one component of a broader framework of health and safety regulations, and it is important to stay up-to-date with any changes or updates. This involves regularly reviewing your practices and procedures, keeping abreast of any changes to the regulations, and ensuring that your training programs are current and comprehensive.
Final Thoughts
Compliance with LOLER is essential for ensuring the safety of lifting operations and protecting employees from the risks associated with lifting equipment. By understanding the key requirements of LOLER, ensuring that lifting operations are properly planned and supervised, and maintaining accurate records and documentation, businesses can achieve compliance and create a safer working environment.